Custom plastic extrusion designed to your industry needs
Custom plastic extrusion designed to your industry needs
Blog Article
A Comprehensive Guide to the Refine and Benefits of Plastic Extrusion
In the large realm of production, plastic extrusion becomes a very effective and important process. Altering raw plastic right into continuous profiles, it caters to a variety of industries with its remarkable convenience. This guide intends to clarify the elaborate actions associated with this method, the sorts of plastic appropriate for extrusion, and the game-changing advantages it brings to the market. The occurring conversation assures to unfold the real-world effects of this transformative process.
Recognizing the Essentials of Plastic Extrusion
While it may appear complex at initial look, the procedure of plastic extrusion is essentially straightforward. The procedure begins with the feeding of plastic material, in the type of powders, granules, or pellets, right into a heated barrel. The shaped plastic is then cooled down, strengthened, and cut into wanted sizes, finishing the procedure.
The Technical Refine of Plastic Extrusion Explained
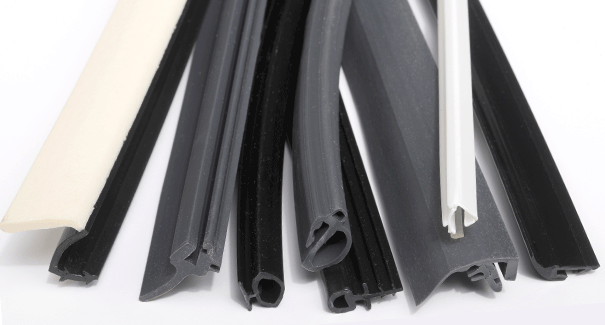
Kinds Of Plastic Suitable for Extrusion
The selection of the best kind of plastic is an important facet of the extrusion procedure. Different plastics offer distinct homes, making them a lot more matched to specific applications. Polyethylene, as an example, is generally made use of due to its inexpensive and simple formability. It provides excellent resistance to chemicals and wetness, making it suitable for items like tubing and containers. In a similar way, polypropylene is another prominent choice because of its high melting point and resistance to fatigue. For more robust applications, polystyrene and PVC (polyvinyl chloride) are frequently chosen for their strength and toughness. These are typical options, the choice inevitably depends on the specific needs of the product being produced. So, recognizing these plastic kinds can significantly boost the extrusion procedure.
Contrasting Plastic Extrusion to Various Other Plastic Forming Methods
Understanding the types of plastic suitable for extrusion paves the method for a wider conversation on how plastic extrusion stacks up against various other plastic developing techniques. Plastic extrusion is unparalleled when it comes to creating continual profiles, such as pipes, seals, and gaskets. It also allows for a regular cross-section along the length of the product.
Trick Benefits of Plastic Extrusion in Production
In the realm of manufacturing, plastic extrusion uses several significant benefits. One notable benefit is this hyperlink the cost-effectiveness of the procedure, that makes it a financially attractive manufacturing approach. Furthermore, this method offers remarkable item versatility and enhanced production rate, therefore raising total production effectiveness.
Economical Production Technique
Plastic extrusion leaps to the forefront as an affordable production technique in production. Additionally, plastic extrusion needs less energy than typical production approaches, adding to reduced functional prices. In general, the monetary benefits make plastic extrusion a highly appealing alternative in the production sector.

Superior Item Versatility
Beyond the cost-effectiveness of plastic extrusion, an additional significant advantage in producing lies in its superior product versatility. This makes plastic extrusion an ideal option for markets that call for tailored plastic components, such as automotive, construction, and product packaging. In significance, plastic extrusion's item flexibility promotes advancement while boosting functional efficiency.
Enhanced Production Rate
A substantial advantage of plastic extrusion lies in its improved production rate. Few other production processes can match the rate of plastic extrusion. Furthermore, the capability to preserve click over here consistent high-speed manufacturing without giving up product top quality establishes plastic extrusion apart from various other methods.
Real-world Applications and Influences of Plastic Extrusion
In the world of manufacturing, the method of plastic extrusion holds profound value. This process is commonly used in the production of a range of products, such as plastic tubing, home window frames, and weather stripping. Consequently, it greatly affects markets like building and construction, product packaging, and automobile markets. Its influence extends to daily items, from plastic bags to tooth brushes and disposable cutlery. The financial benefit of plastic extrusion, mostly its high-volume and cost-efficient output, has actually reinvented manufacturing. The ecological influence of plastic waste remains a worry. For that reason, the sector is persistently pursuing advancements in recyclable and naturally degradable materials, indicating a future where the benefits of plastic extrusion can be retained without endangering ecological sustainability.
Conclusion
To conclude, plastic extrusion is a very reliable and reliable method of transforming resources into varied items. It uses countless advantages over other plastic developing techniques, including cost-effectiveness, high output, marginal waste, and design versatility. Its effect is exceptionally felt in numerous markets such as building, automotive, and customer items, making it a crucial process in today's manufacturing landscape.
Digging much deeper into the technical process of plastic extrusion, it begins with the selection of the proper plastic product. As soon as cooled down, the plastic is cut right into the needed lengths or injury onto reels site here if the item is a plastic film or sheet - plastic extrusion. Contrasting Plastic Extrusion to Various Other Plastic Forming Approaches
Understanding the kinds of plastic appropriate for extrusion leads the means for a more comprehensive discussion on just how plastic extrusion stacks up versus other plastic creating techniques. Couple of various other manufacturing procedures can match the speed of plastic extrusion.
Report this page